Things that rarely occur when producing custom acrylic prints
When producing custom acrylic prints, certain issues can arise that may affect the final product. While we have safeguards and systems in place, even the most diligent processes can sometimes overlook details.
Here are some of these issues:
Banding
Banding in digital prints occurs when there are noticeable lines or bands across an image, typically where color transitions are not smooth. This can be due to a variety of reasons, often related to the printing process or the image itself. Here are the main causes of banding on your custom acrylic print
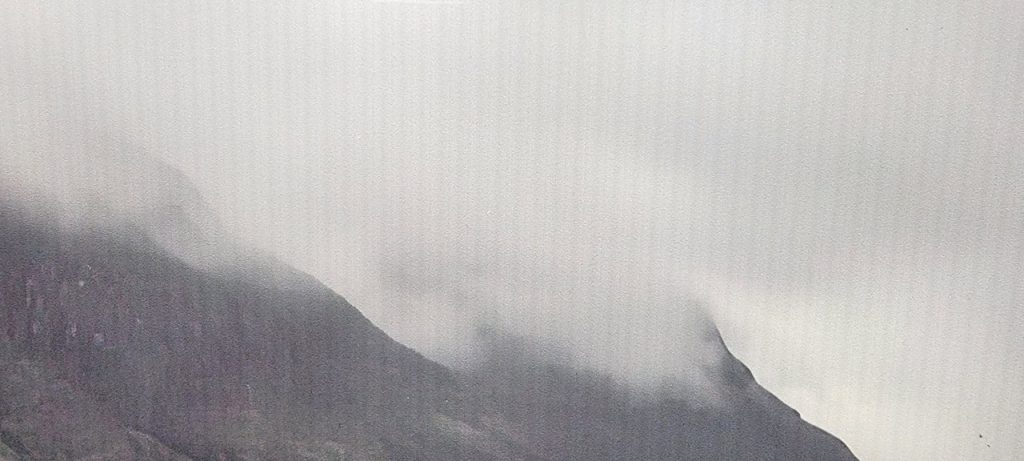
1. Insufficient Color Depth
- Digital printers often use a limited number of colors (such as Cyan, Magenta, Yellow, and Black, or CMYK). If the image doesn’t have enough color depth (like 8-bit or lower), smooth gradients or subtle transitions between colors can become pixelated, causing visible bands.
2. Printer Calibration Issues
- Printers require proper calibration to produce accurate colors. If the printer’s color profiles or settings are not correctly calibrated, it can result in uneven distribution of ink on the paper, which causes banding.
3. DPI (Dots Per Inch) or Resolution Issues
- If the image resolution is too low for the desired print size, the printer may not have enough detail to reproduce smooth gradients. The resolution mismatch can lead to visible stepping between colors in gradients. At big Acrylic the minimum threshhold for dpi is 100. Under 100 will show pixels on your custom acrylic print
4. Ink or Toner Issues
- Inconsistent Ink Distribution: If the printer’s ink cartridges are low or if the toner is not properly applied, it can cause uneven color reproduction, resulting in banding.
- Clogged Print Head: If the printer head nozzles are partially clogged, the ink may not be applied smoothly, leading to visible lines or bands on your cusotm acrylic print
5. Printer Speed and Settings
- Higher print speeds may cause less precise ink placement, leading to banding. Adjusting the printer to a slower, more careful print speed can sometimes alleviate this issue.
6. Paper Type or Quality
- Using paper that isn’t suitable for the printer or that has an inconsistent texture or coating can also cause banding. The paper may absorb ink unevenly, leading to stripes or lines in the print.
7. Color Profile Mismatches
- If the color profile of the image doesn’t match the printer’s color settings, the printer may not blend colors effectively, leading to banding on your custom acrylic print , especially in gradients or subtle color changes. At big Acrylic we work with a CMYK gamut on printer. A color gamut id a wide range of colors you can chaieve by using different color combos like cmyk and Rgb. An Rgb color gamut is much larger the cmyk. It may look amazing on screen but can look muted when producing onto CMYK. This is why ots best to work with CMYK cloaor profile with your images, better consistancy. Read this blog for more info
8. Software Processing
- Certain image-processing techniques or compression settings (like using JPEGs with heavy compression) can lead to banding, especially in areas with smooth gradients.
9. Temperature and Humidity
- Environmental factors like temperature and humidity can also affect the performance of the printer and the paper. Ink or toner might dry too quickly or unevenly, causing visible lines or banding in the print.
Breakages
Box and crate damage
Even the most well-protected acrylic prints can occasionally break. It’s not uncommon to hear about prints arriving with footprints on the box and the acrylic inside shattered. We use top-quality packaging materials to ensure your acrylic print arrives in perfect condition. However, even the most well-protected package can suffer from mishandling, and this issue has become more common since the pandemic.
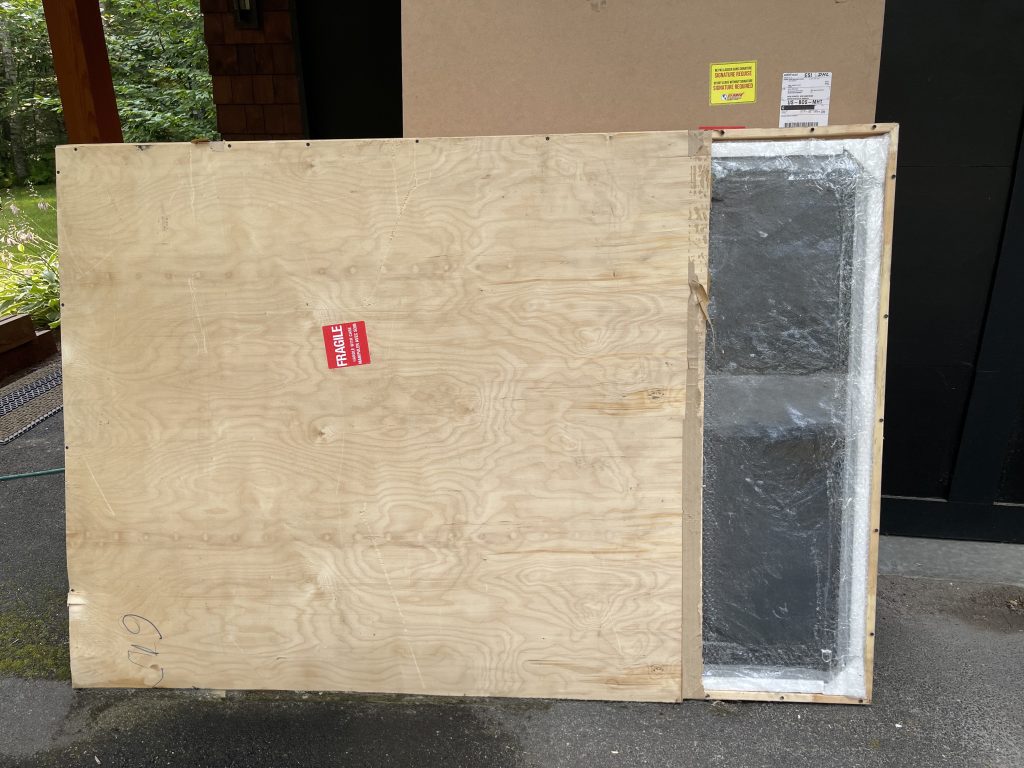
Wrong options
Display
Though it’s rare, mistakes can occur when we create the incorrect display option for a product. If this happens, we rectify it promptly upon customer contact. Customers keep the item they received, and we send them the correct order. This rarely occurs, but it’s all about how you approach solving problems.
Material
Again, this rarely happens but if the wrong medium is shipped the customer casn just contact us and we will redo for free.It’s a win-win situation: you receive two pieces for the price of one.